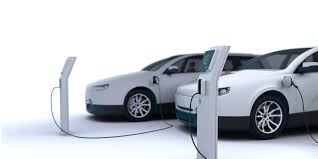
Shape-Shifting Carbon Fiber to Replace Mechanical Systems in Planes and More
The advancement of materials science has opened up new possibilities for improving the design, efficiency, and performance of numerous technological systems. Among the most revolutionary developments is the creation of shape-shifting carbon fiber—a material that can alter its form or properties in response to external stimuli, such as heat, electricity, or stress. This innovation has the potential to dramatically transform aerospace engineering, automotive design, robotics, and various other industries by replacing traditional mechanical systems with adaptive materials that are lighter, more efficient, and more versatile.
In this article, we will explore how shape-shifting carbon fiber works, its potential applications, and how it could ultimately revolutionize industries like aviation, automotive manufacturing, and medical devices.
What is Shape-Shifting Carbon Fiber?
Shape-shifting carbon fiber refers to a composite material made from carbon fiber, which can change its shape or mechanical properties when exposed to specific external triggers such as:
- Temperature: Changes in temperature can cause the material to expand, contract, or bend.
- Electricity: The application of electric fields can alter the material’s structure or form.
- Mechanical Stress: Changes in pressure or force may lead to shape alterations that enhance performance.
- Moisture: Some shape-shifting materials can respond to humidity, allowing for flexibility or rigidity depending on environmental conditions.
This material typically combines carbon fiber with smart polymers or piezoelectric actuators that enable it to respond to external stimuli. The integration of carbon nanotubes or graphene can further enhance its ability to change shape while maintaining its exceptional strength-to-weight ratio.
How Shape-Shifting Carbon Fiber Works
The key to shape-shifting carbon fiber is its composite structure, which consists of carbon fibers embedded in a matrix of resin or polymer. When certain external factors, like heat or electrical impulses, are applied, the matrix (often enhanced with smart polymers) undergoes a structural change. This results in the carbon fibers either moving, bending, or reshaping, depending on the design of the material.
1. Thermal Response
Some shape-shifting carbon fiber composites are designed to change shape when subjected to heat. The polymer or resin matrix in the material can undergo a phase change (from hard to soft, for example) in response to increased temperatures, causing the entire composite to bend or flex in a specific direction.
2. Electroactive Response
Another form of shape-shifting carbon fiber utilizes piezoelectric polymers or electroactive actuators, which change their shape when exposed to an electrical charge. In such systems, the carbon fiber matrix would expand or contract, causing the material to deform and change its configuration.
3. Stress-Induced Shape-Shifting
Shape-shifting carbon fiber can also respond to mechanical stress, such as pressure or tension. The unique arrangement of the carbon fibers and the matrix allows the material to react by shifting shape when force is applied, making it extremely useful for dynamic, high-performance environments like aviation.
Applications of Shape-Shifting Carbon Fiber
1. Aerospace: Transforming Aircraft Design
One of the most promising applications of shape-shifting carbon fiber is in the aerospace industry, particularly in the design and operation of aircraft. Currently, many aircraft systems rely on mechanical actuators to control critical components such as flaps, rudders, and landing gear. These systems add weight and complexity to the aircraft, leading to decreased fuel efficiency and increased maintenance costs.
With shape-shifting carbon fiber, these mechanical systems could be replaced or augmented with adaptive, self-adjusting surfaces. Here’s how:
- Wings and Control Surfaces: Shape-shifting carbon fiber could enable morphing wings that adjust their shape in flight for optimal aerodynamic performance. For example, instead of relying on traditional flaps or ailerons, the entire wing surface could curve or twist in response to aerodynamic forces, improving lift and reducing drag.
- Landing Gear: Carbon fiber materials that can change their shape under stress could be used in landing gear, automatically adjusting to different loads or impact forces, thus reducing wear and improving landing safety.
- Cockpit and Structural Components: By replacing mechanical components with shape-shifting carbon fiber materials, aircraft weight can be reduced, leading to fuel savings and longer operational life. For instance, smart carbon fiber can alter its structure for impact resistance or energy absorption during turbulence or accidents.
2. Automotive Industry: Making Cars Smarter
The automotive industry is also exploring shape-shifting carbon fiber for use in vehicle design. Cars that use this material could have more efficient body structures, improve crash safety, and reduce energy consumption. Here are some examples:
- Crash-Resistant Materials: Shape-shifting carbon fiber could be used in vehicle exteriors or chassis to absorb impact energy and change shape during a collision. This would enhance safety while maintaining the vehicle’s lightweight design.
- Adaptive Body Panels: Automotive parts such as doors, bumpers, and side panels could be made from shape-shifting carbon fiber. These parts could respond to different stresses or environmental conditions, adjusting their properties for aerodynamics or impact resistance.
- Efficiency and Fuel Economy: Cars made from this material could also have adaptive chassis that change shape based on the road or driving conditions, improving fuel efficiency by reducing drag at high speeds or enhancing traction during braking or acceleration.
3. Robotics: Enhancing Flexibility and Functionality
Shape-shifting carbon fiber could revolutionize the design of robotic systems, allowing robots to move more flexibly and efficiently. These materials could be incorporated into robotic exoskeletons, prosthetics, and artificial muscles, giving them the ability to adapt to different tasks or environmental conditions. Some potential uses include:
- Soft Robotics: Shape-shifting carbon fiber could be used in the development of soft robots that are more adaptable and capable of handling delicate tasks, such as in healthcare or manufacturing.
- Wearable Technology: Carbon fiber exoskeletons or assistive devices made from shape-shifting materials could offer greater mobility and comfort for people with disabilities or those requiring physical support.
4. Medical Devices: Advancing Prosthetics and Implants
Shape-shifting carbon fiber could also be applied in medical technology, particularly for prosthetics and implants:
- Adaptive Prosthetics: Prosthetic limbs could be designed with shape-shifting carbon fiber to adjust to various pressures and provide better comfort and functionality for the user.
- Implants: Shape-shifting implants made from carbon fiber could adapt to the body’s changing conditions, improving fit and reducing the need for surgeries or adjustments.
Challenges and Future Directions
While the potential of shape-shifting carbon fiber is immense, there are still several challenges to overcome:
- Manufacturing Complexity: The production of these advanced composites at scale can be complex and costly, particularly for industries like aerospace and automotive that require high standards of durability and precision.
- Cost: Although carbon fiber is widely used in aerospace and automotive industries, the cost of producing shape-shifting composites is still relatively high. Continued advancements in production methods are needed to make this technology more accessible.
- Long-Term Durability: Ensuring that shape-shifting carbon fiber remains functional over extended periods, under various stressors and environmental conditions, is crucial for its widespread adoption.
Conclusion
Shape-shifting carbon fiber represents a significant leap forward in material science, offering the potential to replace mechanical systems in a variety of industries, including aerospace, automotive, robotics, and healthcare. By enabling adaptive materials that can respond to environmental conditions or mechanical stresses, we are moving towards lighter, more efficient, and smarter systems. As technology advances, we can expect shape-shifting carbon fiber to play an essential role in making airplanes, vehicles, medical devices, and robots more functional, efficient, and sustainable.
With ongoing research and technological breakthroughs, the future of shape-shifting carbon fiber looks incredibly promising, and it could reshape how we think about mechanical systems and material design across industries.