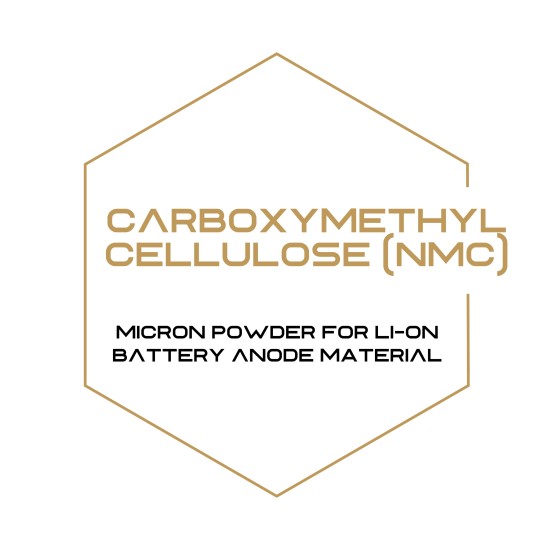
Carboxymethyl Cellulose (CMC) Micron Powder for Li-ion Battery Anode Materials
Carboxymethyl Cellulose (CMC) is a widely used polymer in various industries due to its versatile chemical properties. In recent years, CMC micron powder has gained significant attention in the field of Li-ion battery (LIB) anode materials due to its unique characteristics, such as high water solubility, biocompatibility, and excellent film-forming properties. In particular, CMC is commonly employed as a binder material in the production of anode electrodes for lithium-ion batteries. This article explores the role of CMC micron powder in Li-ion battery anode materials, highlighting its properties, benefits, and applications in the energy storage industry.
1. What is Carboxymethyl Cellulose (CMC)?
Carboxymethyl cellulose is a cellulose derivative, produced by introducing carboxymethyl groups (–CH₂COOH) into the cellulose structure. This modification significantly enhances the solubility of cellulose in water, making it a useful material in various aqueous-based applications. CMC is often produced as a micron powder, which enhances its functionality in several applications, including in Li-ion battery anode materials.
2. Properties of CMC Micron Powder
CMC micron powder possesses several key properties that make it an ideal candidate for use in lithium-ion battery anode materials:
a. High Water Solubility
CMC is highly soluble in water, making it easy to process and handle in the preparation of anode slurries. The water-based slurry is typically used in the electrode preparation process, reducing the need for toxic organic solvents. This contributes to safer, more environmentally friendly battery manufacturing processes.
b. Biocompatibility
The biocompatible nature of CMC makes it suitable for applications in electronic and energy storage devices, where long-term performance and environmental safety are important. As a non-toxic, biodegradable material, CMC is also considered an environmentally sustainable option for battery manufacturing.
c. Good Film-Forming Ability
CMC has excellent film-forming properties, which allow it to create stable films when used as a binder in the anode material. This ability to form strong, flexible films enhances the structural integrity and performance of the electrode during charge and discharge cycles.
d. Viscosity Control
CMC micron powder has tunable viscosity, depending on its degree of substitution and molecular weight. This is crucial in preparing anode slurries with the right consistency to ensure uniform coating and optimal adhesion between the active material and conductive additives.
e. Electrochemical Stability
CMC exhibits good electrochemical stability, ensuring that it can maintain performance during repeated charge-discharge cycles without decomposing or losing its properties. This is critical for the long-term efficiency of Li-ion batteries.
3. Role of CMC in Li-ion Battery Anode Materials
In lithium-ion batteries, the anode is a crucial component that stores and releases lithium ions during the charging and discharging processes. The anode material must be conductive, stable, and able to maintain structural integrity over multiple cycles. Carboxymethyl cellulose, as a binder material, plays an essential role in ensuring the performance of the anode materials, which are often made of active materials like graphite, silicon, or tin.
a. Binder for Anode Materials
One of the primary functions of CMC in Li-ion batteries is to act as a binder in the anode electrode. A binder’s job is to hold together the active material (e.g., graphite or silicon), conductive additives, and the current collector. CMC’s water-based properties make it easier to prepare slurries without the need for harmful organic solvents, which improves the environmental sustainability of the production process.
b. Improving Structural Integrity
The film-forming properties of CMC enable the formation of a cohesive film that enhances the adhesion between the active material and the conductive additives. This improves the overall structural integrity of the anode, preventing the active material from detaching during cycling. For silicon-based anodes, which experience significant expansion and contraction during charge-discharge cycles, CMC helps to maintain structural stability and prevent cracking.
c. Enhancing Electrochemical Performance
CMC contributes to the overall electrochemical performance of the anode. The binder enhances the distribution and homogeneity of the active material, which in turn leads to more efficient lithium-ion insertion and extraction. Additionally, CMC’s electrochemical stability ensures that the binder does not interfere with the battery’s charge and discharge processes, maintaining high efficiency over extended use.
4. Benefits of Using CMC Micron Powder in Li-ion Battery Anodes
The use of CMC micron powder in the manufacturing of Li-ion battery anode materials offers several key benefits:
a. Environmental Sustainability
CMC is derived from natural cellulose, which is abundant and renewable. The use of water-based systems in the production of anode materials reduces the reliance on harmful organic solvents, contributing to cleaner, more environmentally friendly battery manufacturing processes. Additionally, CMC is biodegradable, making it a sustainable choice for next-generation batteries.
b. Cost-Effective and Scalable
CMC is relatively inexpensive compared to other binders used in battery manufacturing, such as polyvinylidene fluoride (PVDF). It is also highly scalable, which means it can be used in large-scale production processes without significant cost increases.
c. Enhanced Battery Life
CMC’s ability to form strong, flexible films helps maintain the structural integrity of the anode material during cycling, which is essential for enhancing the cycle life of the battery. As lithium-ion batteries age, the anode material can degrade, leading to a decrease in performance. CMC’s binder properties help mitigate this issue by ensuring that the anode remains stable over time.
d. Improved Safety
Water-based slurries that use CMC as a binder reduce the use of flammable and toxic organic solvents, improving the safety of the manufacturing process. Additionally, CMC’s electrochemical stability contributes to the overall safety of the battery during operation by preventing unwanted reactions with the electrolyte.
5. Challenges and Considerations
While CMC has numerous advantages, there are some challenges to consider when using it in lithium-ion battery anodes:
a. Compatibility with High-Capacity Anode Materials
As battery technology advances, high-capacity anode materials such as silicon and tin are being explored to replace conventional graphite anodes. These materials undergo significant volume changes during charge-discharge cycles, which can lead to binder degradation and loss of capacity. Researchers are working on improving CMC formulations to better accommodate these high-capacity materials and enhance the cycling stability of silicon-based anodes.
b. Modification and Optimization
To fully exploit the potential of CMC in lithium-ion battery anodes, it may be necessary to modify or optimize its properties, such as its degree of substitution and molecular weight. Research is ongoing to find the ideal CMC formulations that provide the best balance of viscosity, adhesion, and electrochemical performance for different types of anode materials.
6. Future Directions
As the demand for more efficient, sustainable, and cost-effective energy storage solutions grows, the role of CMC micron powder in Li-ion battery anodes is expected to expand. Future research may focus on:
- Developing advanced CMC derivatives: By modifying CMC’s chemical structure, researchers can enhance its properties for use in next-generation batteries, including high-capacity anodes.
- Hybrid binders: Combining CMC with other materials like graphene, carbon nanotubes, or conductive polymers could further improve the performance and cycle life of Li-ion batteries.
- Solid-state battery applications: CMC may also find use in solid-state batteries, which promise higher energy densities and improved safety compared to conventional liquid electrolyte-based batteries.
7. Conclusion
Carboxymethyl cellulose (CMC) micron powder is an increasingly important material in the production of lithium-ion battery anodes. Its unique combination of properties, such as water solubility, biocompatibility, and excellent film-forming ability, makes it an ideal binder for anode materials, especially in environmentally friendly, water-based slurries. With the growing demand for advanced energy storage solutions, CMC is expected to play a crucial role in the development of more efficient, sustainable, and cost-effective lithium-ion batteries. Further research and optimization will likely continue to improve its performance, paving the way for next-generation battery technologies.