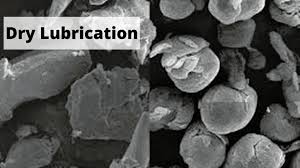
Dry Lubant Agents: The Silent Heroes in Friction and Wear Reduction
Dry lubricant agents are materials used to reduce friction and wear between two surfaces in relative motion without the need for liquid lubricants. These agents function as solid films or coatings and are typically applied in environments where traditional liquid lubricants may not be effective or desirable, such as in high-temperature, high-pressure, or vacuum conditions. This article explores the various types of dry lubricants, their properties, applications, and advantages.
What Are Dry Lubricant Agents?
A dry lubricant is any substance that reduces friction between moving surfaces without the need for liquid-based lubrication. Unlike conventional lubricants, which require a fluid film to separate the surfaces and minimize direct contact, dry lubricants function through solid-phase mechanisms. These materials form thin, stable films that reduce friction, prevent wear, and in some cases, provide corrosion resistance.
Dry lubricants work by either chemically bonding to the surface or by creating a thin, low-friction layer that remains intact under various conditions. Unlike wet lubricants, dry lubricants are often used in extreme conditions where conventional oils or greases cannot perform, such as in high-temperature environments, vacuum chambers, or clean room settings.
Types of Dry Lubricants
There are several types of dry lubricant agents, each with distinct properties, characteristics, and applications. Some of the most commonly used dry lubricants include:
1. Graphite
- Graphite is one of the oldest and most widely used dry lubricants. It is composed of carbon atoms arranged in a hexagonal lattice structure, and its layered arrangement allows the layers to slide easily over each other, providing excellent lubrication.
- Properties: Graphite is a good conductor of electricity and performs well in high-temperature and high-pressure environments. It is also chemically inert and stable under most conditions.
- Applications: Graphite is commonly used in applications such as high-speed bearings, drill bits, automotive components, and furnace seals.
2. Molybdenum Disulfide (MoS2)
- Molybdenum disulfide (MoS2) is another widely used dry lubricant, known for its exceptional load-bearing capacity and ability to reduce friction under extreme pressure. MoS2 has a unique crystal structure that allows its layers to slide past each other easily.
- Properties: MoS2 excels in both high-load and high-temperature environments. It is chemically stable and resistant to oxidation and corrosion. MoS2 is also insulating, making it useful in electronic and electrical applications.
- Applications: MoS2 is commonly used in aerospace, automotive, heavy machinery, and industrial equipment such as gears, bearings, and valve components.
3. Tungsten Disulfide (WS2)
- Tungsten disulfide is another solid lubricant similar to MoS2 but with superior performance at extremely high temperatures and under vacuum conditions.
- Properties: WS2 has a low coefficient of friction and excellent wear resistance. It remains effective in vacuum and high-vacuum environments, and it can also withstand extreme temperatures, ranging from cryogenic to over 1000°C.
- Applications: WS2 is widely used in spacecraft, vacuum pumps, semiconductor processing, and high-performance machinery that operates under extreme conditions.
4. PTFE (Polytetrafluoroethylene)
- PTFE, commonly known as Teflon, is a synthetic polymer that is famous for its non-stick properties. It is often used in dry lubrication applications where a smooth, low-friction surface is required.
- Properties: PTFE has excellent chemical resistance, high thermal stability, and an extremely low coefficient of friction. It can operate over a wide temperature range and is non-reactive with most chemicals.
- Applications: PTFE is commonly used in food processing, medical devices, seals, gaskets, and sliding bearings in environments where contamination is a concern.
5. Boron Nitride (BN)
- Boron nitride is a synthetic compound that exhibits excellent lubrication properties at high temperatures, with its performance similar to graphite. BN is particularly useful when traditional lubricants fail due to heat or environmental factors.
- Properties: Boron nitride has excellent thermal conductivity, is chemically stable, and performs well in both high- and low-temperature environments. It is also an electrical insulator, which makes it valuable in electrical applications.
- Applications: BN is used in electronic components, heat exchangers, aerospace, and nuclear industries for applications requiring lubrication at extremely high temperatures.
6. Calcium Carbonate (CaCO3)
- Calcium carbonate is used as a dry lubricant in certain industrial applications, particularly in plastic processing and as a finishing agent in rubbers.
- Properties: It offers moderate lubrication and can be used as a filler in formulations to improve the performance of products without significantly changing their base properties.
- Applications: Commonly used in the automotive, construction, and textile industries for rubber compounding, coatings, and plastic materials.
7. Ceramic-Based Lubricants
- Ceramic-based lubricants typically use silicon carbide or alumina particles embedded in a matrix. These dry lubricants are known for their hardness, high-temperature stability, and abrasion resistance.
- Properties: Ceramic lubricants can withstand extremely harsh conditions, such as high-speed machinery, cutting tools, and machining operations. They provide a solid film that improves wear resistance.
- Applications: Used in cutting tools, machinery bearings, and industrial equipment subject to high wear rates.
Advantages of Dry Lubricants
Dry lubricants offer a range of advantages over traditional liquid-based lubricants. Some key benefits include:
- No Contamination: Dry lubricants do not leak, drip, or evaporate, making them ideal for sensitive environments such as clean rooms, vacuum chambers, and food processing industries where contamination is a concern.
- Wide Operating Temperature Range: Many dry lubricants, such as MoS2, WS2, and graphite, can operate effectively at very high temperatures (up to 1000°C or more) where liquid lubricants would degrade or evaporate.
- Enhanced Durability: Dry lubricants can form stronger bonds with surfaces, leading to longer-lasting protection against wear and tear, reducing maintenance costs.
- Reduced Environmental Impact: Dry lubricants are less likely to spill or cause environmental damage compared to liquid lubricants, which may leak or pollute surrounding environments.
- No Need for Oil Changes: Since dry lubricants do not require a supply of oil, the need for regular maintenance such as oil changes and disposal is eliminated.
Applications of Dry Lubricants
Dry lubricants are used in a wide range of industries where traditional liquid lubricants are ineffective or impractical. Common applications include:
- Aerospace: Components such as landing gears, seals, and actuators use dry lubricants to perform in high-stress and high-temperature conditions found in aviation and space exploration.
- Automotive: In engines, brake pads, bearings, and seals, dry lubricants are often applied to improve performance and durability.
- Electronics: Graphene, MoS2, and BN are used in semiconductor manufacturing, microelectronics, and solar panel coatings where friction and heat dissipation need to be controlled without adding electrical conductivity.
- Manufacturing and Heavy Machinery: Gearboxes, conveyors, and cutting tools benefit from dry lubricants, which help reduce friction and extend the life of mechanical parts.
- Military and Defense: Dry lubricants are used in weaponry, armored vehicles, and defense machinery, where reliability and performance in extreme environments are critical.
Challenges and Limitations
While dry lubricants offer many benefits, there are some limitations and challenges to consider:
- Limited Load-Bearing Capacity: Some dry lubricants may not perform as well under extremely high loads compared to liquid lubricants. This may limit their use in some high-load applications.
- Surface Preparation: To ensure maximum performance, the surface preparation and application of dry lubricants must be precise. Improper application may result in ineffective lubrication and premature wear.
- Environmental Sensitivity: Some dry lubricants, such as graphite and MoS2, can be sensitive to moisture, which can affect their performance.
Conclusion
Dry lubricants play a critical role in reducing friction and wear in various industries. Their high-temperature resistance, chemical stability, and long-lasting performance make them ideal for extreme environments where liquid lubricants may fail. From aerospace to electronics, dry lubricants provide solutions for efficient, sustainable, and reliable machinery operation. As research and development continue to improve these materials, the use of dry lubricants is expected to expand, offering even more innovative and versatile applications in the future.